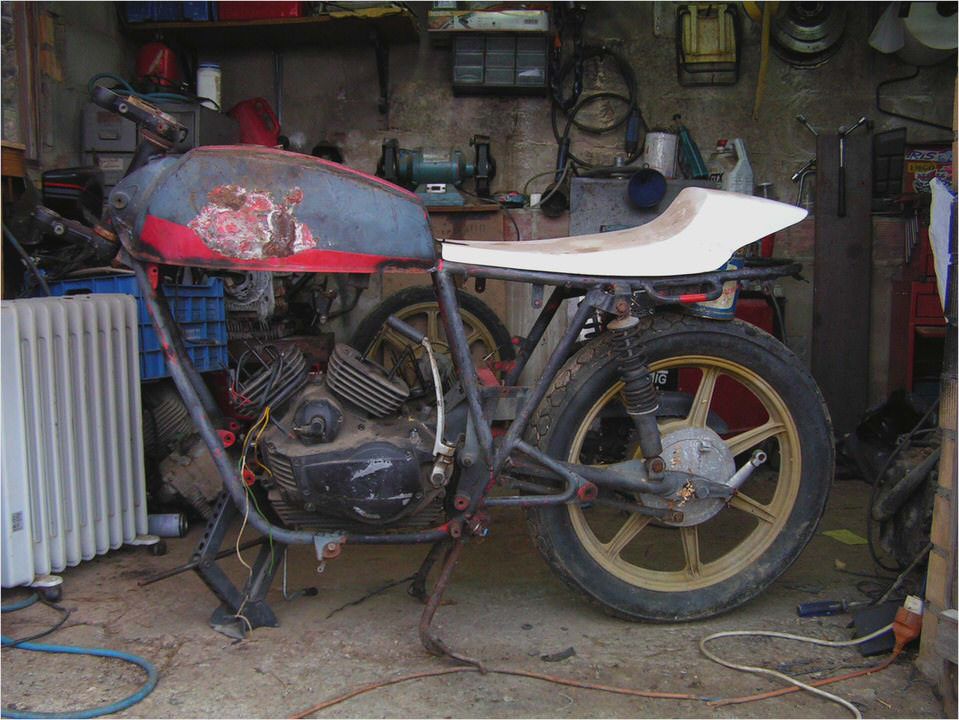
Morini race bike
OK. The plan is to build a cheap race bike and compete in the CAV (Andalusian classic under 500cc race series). I decided on a Morini because a friend gave me a 3 1/2 sport that had been sitting in a friends yard for between 9 and 15 years. The motor was seized, but freed off after a bit of rocking back and forth in gear. The tank has rusted through underneath and all the wheel bearings have seen better days.
The picture above is how it looked after I took it out of the van at my house.
I have been thinking about using a 501 motor (from the new york), but they are actually 507cc, so would push me in to the unlimited class and I would be competing with 1000cc guzzi’s, bmw’s and a couple of CB900 honda’s. So I have started looking in to bringing the cc’s down to sub 500.
The original 500 Morini’s where actually about 478cc +/- (I can’t remember the exact number ), but the 501 bottom end is stronger, after you have swapped the timing side bush for a roller bearing. So how about putting the 500 barrels and pistons on to the 501 bottom end. Not impossible, but needs thinking about.
The problem is that the outside diameter of the spigot (the bit of the cylinder that sticks out the bottom of the finned part of the barrel and locates in the crank case mouth) is about 2mm smaller on the 500 than it is on the 501. This doesn’t sound like a big deal, but actually is. with the 2mm gap you lose the rigidity of the close fit and this makes the whole motor weaker with the added problem of potential barrel movement at high rev’s.
There was also the price. Second hand barrels and pistons for the 500 from NLM (the only place that had them)came in at 136 GBP plus vat and postage (EEKK), per cylinder and they would need a new set of rings, which are unavailable at the moment.
So the plan is to prepare a 350 motor with the parts I have and give it a flow job. I am pretty certain that the 3 1/2 motor is a sport, so I have a lumpy cam and if I can lay my hands on some 500 heads I will have the bigger valves as well and can run the 28mm dellorto’s that I have had bored to 30mm.
This will put me at a disadvantage as the other bikes all have more cc’s than me, but the Morini will hopefully weigh in at around 120kg, which is a good bit lighter than most of the bikes out there. I will then prepare a bottom end and hope that a set of barrels comes up at a reasonable price and that rings for said barrels become available again.
The braking department has already been sorted. I will be keeping the single disc set up, but will be using a 300mm disc that weighs less than the original(I will post the weights when I get the 300mm disc back from the engineer). The Grimeca caliper hasn’t been inspected yet, but I suspect it has seen better days, so will be replaced with a FZR caliper (if the regs allow it.
I’m still awaiting the definitive set of regs for the coming year) and if I can’t use the FZR set up I will use a FZ750 caliper(because I have lots of them) and they are only twin piston, which seems to be the norm for classic race bikes.
16/11/10
Well I managed to get out in the shed for a half day over the weekend and started stripping a Dart bottom end that I picked up along with a 350 cc Kangaroo. All went well until I came to take the castellated nut off of the oil pump worm gear on end of the crank, someone had already given it a bit of a chiseling, so the correct tool is out of the question. after attacking it a number of times with various hammers and punches/chisels I gave up, as I didn’t want to damage the thread and I wasnt entirely sure that it wasn’t a left hand thread. ho-hum.
I started looking at the frame (I took the engine out last week and removed the forks to see if some Guzzi V50 ones would fit, They did but where about 25mm shorter and I want to raise the bike up to give it more ground clearance so took them out again), but it was raining outside and I had pulled in the Kangaroo I had just bought. There was very little room to move about, as you can see from the picture. The 3 1/2 frame is behind the Kangaroo and in front of the Guzzi engine.
So I decided to get on the lathe and do a little lightening of pieces and cleaning up of rough surfaces.
First up was the alternator. As you can see from the picture, I machined off the starter clutch and am very pleased with the result. I used the scabbiest one I have just in case it all went pear-shaped.
But it will clean up nicely I think.
Then made up some alloy foot rests and started trying to machine the face of the primary drive gear that sits behind the clutch. This was difficult as my lathe is very small and had to cut the angle by eye. I tried this for a while, but gave up when I snapped the second tip on the tool.
So will be taking it to a local engineer with a 3 phase big lathe.
21/11/10
This weekend I managed to get out in to the bike shed a fair amount and apart from a couple of hours of dithering feel I have made some progress.
The dither took hold because I hadn’t made a list of priorities, all important when under taking a project like this, but always seems to get forgotten or put off until it’s too late. In the end I just grabbed the petrol tank, angle grinder and welder and using an old superdream tank as a donor, started hacking all the rusty bits out of the bottom of the Morini tank. As you can see it does have a certain lace curtain quality that isn’t conducive to holding petrol.
There was also a sizable chunk of filler on one side that I attacked with a screw driver and hammer. There must have been about a kilo of dried filler and once it was removed there was a good dent that needed knocking out. So while I was chopping out the rust I also chopped a large section of good metal out to gain access to the affected area and regain some of the original capacity of the tank.
After that it was just fabricating pieces of superdream tank to fit the lacey parts of the Morini tank. It doesn’t look perfect but good enough. At the end of the day it’s going to get thrown up a race track a good few times if my usual form is to be maintained.
After the tank was finished I decided to work out the look of the bike and give myself some motivation to get the seat unit fitted and all the ancillary bits stuck on. I have thought long and hard about the tracks that we will be racing at next year and have come to the conclusion that I will set the bike up with clip-ons and leave the cables long enough for some motor cross bars.
My thinking is that some of the circuits are pretty tight, like Monty Blanco, and they favour the bikes with normal/MX bars as you can get more leverage and keep better control through the corners. But they also race at Jerez, which is a big track with only a couple of slow corners and lets face it the Morini is going to be flat-out through most of the track. So I want to be tucked down with clip-ons and a fairing.
So I am going to fit a flat track seat unit I have had kicking about for a couple of years and I also have some scabby old race fairings that I will look at at a later date. This is a preview of Frankensteins Morini. Pass me the welder will you Igor.
Next up is to strip the sport motor and use the cam with the Dart bottom end, which I don’t think has covered many miles as it is in as new condition. As soon as I took the heads off of the sport I realised that I will have to look in one of the other motors for barrels and pistons, as at least the front pot has seen better days.
OK. move on to the clutch. as soon as the cover came off I realised that I may have to have a chat with the clutch with the angle grinder and a cutting disc. all the clutch spring screws are rusted on to their respective bolts and the factory tool isn’t moving them. This picture was taken after I had wire brushed the worst of the rust off, scrapped all the dust and debris out of the case and sprayed lots of WD40 all over it.
Out with the hammer and drift. The clutch screws mock my efforts to unscrew them and snigger at the mole grips as they slip from the few millimetres of protruding clutch screw and leave a blood blister on the flesh of my hand. Bugger.
I leave the screws to marinate in WD40 and head for the fridge for a medicinal beer.
7/12/10
As you have probably noticed, I haven’t posted anything for a while. This is because we have had a death in the family and have had to come to the UK for the funeral. I did quite a bit of work on the heads before I left and will give you a full blow-by-blow account of that when i get back home to sunny Espana.
I also must say that I have enjoyed the snow that we have had here in Blighty, but will be glad to get back to the relative warmth of Andalusia.
12/12/10
After a few hours trying to coax the clutch spring nuts to loosen I realised that it just wasn’t going to happen with out the help of my trusty angle grinder. A few of the studs that the nuts are on had come un welded from the back of the clutch centre and where spinning freely.
So I cut in at a shallow angle and managed to cut the top off of the mushroom shaped nuts and release the spring from underneath and, with no small amount of difficulty, remove the clutch plates, which bear an uncanny resemblance to artifacts that have been retrieved from an ancient ship wreck. But they won’t be wasted as I will turn them in to a clutch holding tool.
I then found that the clutch centre was also reluctant to part company from the shaft, so fabricated a puller from an old (and distorted) clutch outer plate. By bolting it to the clutch centre with the mushroom nuts and some large washers you can then wind in the centre allen bolt and pull off the centre.
Then it was a case of removing all the other bits and pieces, which was very simple compared to the clutch, and split the cases. I was a little worried about the state of the cam, but upon inspection it was found to be in very good condition. I can’t find the “S” that is supposed to be stamped on the cam centre, but have read that they sometimes are very faint or non-existent.
I then compared it to the “M” cam and the “S” cam has a more radical profile.
I then attacked the extremely scabby clutch cover case from the sport with a rotary wire brush on my drill and was surprised to find that the remaining black paint that is stuck to the case can be removed pretty easily. Unfortunately I didn’t get a picture of it before I attacked, but here it is after a savaging with the drill.
Next up are the cylinder heads. I have had a stroke of luck on this score. When I purchased the Dart bottom end along with the Kangaroo there was a cylinder head along with some odds and ends. The head is (I assume) a dart head as it has the larger valves, but there was only one of them.
I then removed the heads from the Kangaroo along with the sport heads took them all to the tuning area/kitchen table(I have a very understanding wife).
There I measured the valves and found that the previous owner had fitted one of the Dart heads to the Kangaroo. This was a pleasant surprise, as I thought that i would have to use a pair of the smaller valve heads or, heaven forbid, buy another Dart head.
Once the valves where out of the head it was found that the guides where in good condition. The Morini heads already have well designed ports, so it is just a case of cleaning up the casting marks and blending in any steps that are at the back of the seats or on the intake stubs. I also found on the internet a design for an alleged factory exhaust system which I will copy and see how it performs.
The inside diameter of the pipe is 27mm and I will also enlarge the exhaust port exit to 27mm so there are no steps, as any step or sudden change in diameter will cause a pressure wave to go back up the pipe to the valve. These pressure waves can be a good thing. like on lower engine revs you can build them in to cause a pressure wave that stops the incoming charge (petrol/air mixture coming in the inlet valve) escaping out of the exhaust valve on overlap (both valves are open at this point) . But if you don’t know how to build these in accurately, which I don’t without lots of dyno time, I think it’s best if there are as few steps/changes in diameter as possible.
I am also surprised at the quality, or lack of it to be exact, on the cylinder heads. In this picture of a cleaned cylinder head you can see the porosity (air holes) in this casting.
By the way I learned a trick from a friend that owns a cylinder head repair shop. You can use an orbital sander to clean the face of Heron heads (flat head with vertically mounted valves, like the Morini). It is trickier to do on hemi heads (heads with the combustion camber in the head, not like the Heron that has the combustion chamber in the piston) as it is easy to chamfer the edges and make the gasket face slightly curved, resulting in possible gasket failer.
To clean the valves up I put them in the lathe and used some course wet and dry (60 grit) to get the worst of the carbon off. Then progressed to 180 grit. Heres some I made earlier (Blue peter tuning.
If you are not of a certain age and English, you won’t have a clue what I’m talking about).
As you can see, the inlet valve is also quite pitted, whether from rust or bad production techniques I don’t know. But looking at the exhaust valve, which has almost no marks on it at all, I would say that the latter is most likely. You can get the same results as I have with the lathe, by putting an electric drill in a vice and putting the valve in the chuck.
If there is a large build up of carbon on the valve you can use a small screw driver like a lathe tool to clean it off before you go to it with the wet and dry. Now I clean up the ports with my trusty Dremel and flexible drive. I have found that if you use cutting tools on aluminium they clog up and stop cutting.
If you dip your cutting tool in to vegetable oil regularly it doesn’t clog up (it also adds a distinct flavour and texture to fried foods if, when you have finished you use the remains for cooking).
29/12/10
Well, after not a lot getting done over the last couple of weeks there has been a positive flurry of activity over the past couple of days. First up was to get the seat unit mounted and for this I rummaged in my steel pile and came up with a length of 16mm X 3mm mild steel. A lot of people seem to think that you need to make seat supports out of RSJ’s, but I have found that you can use very little material to make a solid mounting.
In fact if you have a look at most production bike seat mounts you will see that they are made of pressed up steel sheet of less than 1mm. I made up a front support and held it along with the seat in the position that it would be welded and then spotted it in place. I could then make up the rear support and do the same. I made that sound easy and it was apart from the part where you have to hold it all in place whilst spotting it with the welder.
For this you could do with an assistant from the audience or grow another couple of arms. Once I was happy with the angle of the supports (you want them flush with the base of the seat or it may split the seat base when you tighten the fixing screws down) I started makin up the lateral supports. These where a little trickier to make as the base of the seat has a gentle curve.
Armed with a ball pane hammer and an anvil( a small section of railway track) I worked the metal until it fitted the curve of the seat. I then tacked that in, placed the seat on top and checked from underneath that it sat snuggly on the supporting frame I had made. Once I had made the odd adjustment with the hammer I welded it all up. I also had a rummage through my threaded boss container (an old peach tin) and found a couple of 6mm bosses that I thought would be good fixing bolts.
These I welded in to the inner corners of the support frame.
Now to make up the front mounting plate for the seat base. This will be made from some scrap sheet that was once part a an FZR 1000 silencer. I put the seat base on the support frame in the position I wanted it mounting and then drew around the inside of the supporting frame.
I now had the position and dimensions of the mounting plate. I chopped the plate out with the angle grinder, bent it up in the vice and pop riveted it in to place.
Now it’s a simple job of sliding the mounting plate under the front of the support frame and centralise the seat. I then get a tin of black spray paint and, with the seat in the exact place I want it mounted in I spray up through the 6mm bolt holes in the bosses that I welded to the inside of the frame. This gives me the points at which I have to drill.
That done and hey presto I have a seat on my bike.
With the seat mounted and the clip-ons on I can decide where I want the foot pegs. I will mount the pegs slightly forward of their ideal position for clip-ons as I will be using the motocross bars most of the time. I make the mounting plate out of 40mm X 3mm. Again, this may not seem like a lot, but it only spans a short distance.
They end up being mounted at what looks like a weird angle, compared to the frame, but the passenger peg loops, which they are welded to, are actually splayed and not vertical.
Next up is the gear change and rear brake. I haven’t been looking forward to this at all. I will explain. I have mostly been riding Italian and Japanese bikes for the past 30 years (left foot gear change). Before that I rode a lot of British bikes(right foot gear change).
I briefly owned an 350cc Enfield, about 12 years ago and whilst chasing a couple of 600cc sports bikes through some twisties (I know it’s sad and I do take my medication, but some times The sickness over comes me). Anyway I was concentrating on the road and slammed the back brake on whilst trying to change down the box (I was slightly banked over at the time and the resulting slide added a whole new dimension to the word exciting).
Also, about 23 years ago I had a BSA A65 650cc parallel twin (right foot change and 1 up the rest down) as my nice bike and a Suzuki GSX 250 as my everyday transport (You can’t use an A65 for everyday transport as they tend turn engine internals into externals). Again I was out with a few friends and merrily thrashing the GSX, when having dived round the outside of one of said pals and accelerating out of the corner changed down instead of up, whilst in the red zone of the rev counter.
There was no damage done (those engines really are incredibly strong) but I thought about what would happen if I did the same on the A65. I think there would be a wailing and gnashing of teeth and devastation of biblical proportions. Which brings me back to the Morini, which is, as you have probably guessed, right foot change.
A number of people have said to me that I should just get used to it and stop whingeing. But this doesn’t stop the thoughts of bent valves and sliding down the track on my arse. I therefore decided to swap from the Satanic right to the saintly left (although the word sinister comes from the latin for left and refers to left-handed people who were considered evil.
This is ridicules as we all know that it is people with red hair that are the work of the devil). To which end I have considered a number of different systems for the swap. I have settled on a system that only incorporates 2 rose joints and a shaft. I had an old Kangaroo chassis knocking about and most of the running gear, which uses a shaft to take the gear change from right to left.
I dug this out and hacked off the sleeves that it rotates in. I then rummaged in my foot control box and found a Cagiva elefant gear lever that fits the splined end. Next up was to remove the original gear lever from the non splined end with the angle grinder (wonderful tool) and popped the shaft in to the lathe. Having had a firtle in my spacer container (old tomato tin) I found a likely looking suspect for the job of supporting the non splined end once it had been turned down.
I then turned the non splined end down, leaving a small section to act as a stop and drilled and tapped a hole in the centre of the end so that I could fit a 6mm Allen bolt and large washer. This would hold the bush that I will make up to weld to the frame and stop the shaft from sliding left or right. On the other end of the shaft I will employ the sleeve that I hacked from the frame. Here are the parts that I turned up in the lathe.
I did take a picture of all the components, but it seems to have been kidnapped by aliens (more common than you think).
I now held it in position under the bike with a scissor jack to see where I want the lever to be on the left and how the linkage will be on the right. Now it needed a small plate with a hole to fix the rose joint to. I measured the plate on the gear change shaft and copied the dimensions on to the plate I made then welded it to the shaft.
Put it all back on the scissor jack and get the final position (making sure it was as parallel as possible to the frame) then weld it all up. A small piece of 6mm threaded bar was used between the 2 rose joints and Robert is your mother’s brother.
4/2/11
Well, it has been a long time since I posted anything, but things have been getting done admittedly not as many as I would have liked, but you can’t have it all. The original plan was to have the bottom end together,rear brake lever fabricated and fitted. I also wanted to go to Seville to get the barrels and pistons measured and decide which ones where to be used.
Well that all got blown out of the water with the decision to sell our house and move farther south to a village called Valverde del camion, where we have a language school. So I have been repainting the house and doing all those small jobs that I have been avoiding, like refitting the bedroom floor ,building the on suite bathroom and building the extension to the back of the house. As I said small jobs. As you can imagine this has knocked a hole in my free time.
But I have managed to finish the internals of the bottom end and I am planning on blagging a morning to put it together in the next week (or so I hope). First up was the cam pulley, which weighed a hefty 334 grams. a tad over kill. I trimmed this down to 224 grams and could probably take some more off of that.
But the thought of the pulley breaking at 10,000 rpm and the ensuing carnage gives me nightmares.
Once it was turned down I left it on the bench and it gained a little surface rust which has come out in the photo a lot worse than it actually is. ( I have just got off the phone to Alex at North leicester motorcycles and he told me that he also made a lightened cam pulley and it just doesn’t work. The reason that the cam pulley weighs so much is that the cam belt doesn’t have a tensioner and the weight of the pulley acts as a damper for the cam, damping out the action of the cam and keeping it all flowing smoothly.
He found that when he fitted the light pulley the ignition was moving around quite drastically because of belt stretch. Well back to the drawing board.)Next up is the clutch . I took the outer and gave it the Swiss cheese look, which is so fashionable on a race bike.
This didn’t reduce the weight as much as I would have thought. The standard weighing in at 444 grams. whilst the ventilated version weighs 412 grams. Which at the end of the day is pretty negligible.
I have heard of people who have become obsessed with weight reduction on bikes and have spent many hours drilling virtually everything and slimming parts down in lathes to the point where the strength of the chassis and internal engine components has been compromised. I now see how this addiction to weight reduction takes hold. But even with the two parts I have lightened here I have only saved myself 140 grams.
If I go to the toilet and have a dump before a race I would save more weight than that and I wouldn’t have to spend hours doing it (obviously, depending on what I ate the night before. But lets not go there). I wanted to lighten the clutch inner as I think some serious weight could be removed from it, but found that it is made from a hardened steel that guffawed at my attempts to penetrate it.
I took it to a local engineer to try his pillar drill, which, I’m not saying is old, but I have heard was used in the construction of the Ark. which along with a cobalt drill bit should be able to savage most types of steel. Not so. Again the clutch centre scoffed at my attempts to drill holes in it and I had to admit defeat.
Both myself and the engineer where a little surprised at the quality of the steel used for the clutch centre and I can’t understand why I have a couple that are completely chewed up. I would have thought that with the plates being made of mild steel and the centre being made of some sort of hardened high carbon steel and the plates would be as putty and mangle accordingly. Not chew up the centre. It’s probably just one of those things. So next up is to polish the crank.
I wound masking tape around all the journals 3 or 4 times and then did the same with insulation tape. I really didn’t want to damage any journals and have to use one of the other cranks. I started with a die grinder grinding stone in my drill, then moved on to a flap wheel and finally a 180 grit scotch bright bobbin.
I have posted a picture of the Bobbins, but not the die grinding stone as the last one I had exploded when I was grinding the crank (I think there was a fault or air bubble in the stone). I always wear safety glasses and on this occasion was very glad I did.
Here is a picture of the crank half done.
As you can see I am only removing the minimum material from the crank webs to get a nice polished finish on it. After many hours of grinding, sanding and polishing it looks like this.
Apart from this very little has happened in the bike shed. I have provisionally fitted the new top yolk with the handle bar clamps along with the motocross bars, but still haven’t got around to fabricating the rear brake pedal.
I have started making a list of all the bearings in the motor and will post them in the Morini tech section once I have a full list One other problem that has made me reluctant to do any major surgery is that I have heard that the regulations have been radically changed (the only one I have been able to confirm is that the entry date has been changed from the end of ’82 to the end of ’79 which no-one foresaw) . I have called the FAM (the ruling body for motorcycle racing in Andalusia) and was told that the new reg’s would be published in the first week of January. This of course I didn’t believe and so I was proved correct in my assumption.
I called again at the end of January to be told that the Regs would be published between the 14th and 16th of February. I am not holding my breath. I spoke to one of the other guys that race in this series and he told me that last year the reg’s where published at the end of march, when the first race was at the beginning of May. WELCOME TO ANDALUSIA.
You do get used to this kind of blatant lying and accept it. But another thing you get to accept is that most rules only apply to you (as in anyone) if you take them seriously, which of course no one does. Last year the guy that won the last race had a complete LC front end on his yamaha XS400.
It was obvious that it wasn’t the original front end as the wheels where different, but no one cared because everyone is bending the rules to some extent. One guy has a honda 500/4 with complete race body work. The regs state that you must use the orignal petrol tank and that the fairing must be of a similar in appearance to the original one fitted.
They never fitted a fairing to the 500/4 or for that matter any bike of the 70′s, so how can you fit a fairing to pretty much any bike of that era? So as you can see the rules aren’t really rules, more guide lines that can be ignored if you so choose. Oh, and this applies to most aspects of life in Andalusia. In the UK rules are black and white. Here everything is a murky grey.
It certainly keeps you on your toes.
5/3/11
Well it’s all gone a little pear shaped at the moment. As I said before, we have finally decided to sell our house and move a little farther south. So I have been repainting the house, relaying floors etc in preparation for the estate agents (or the nearest thing we have to an estate agent over here) taking photos.
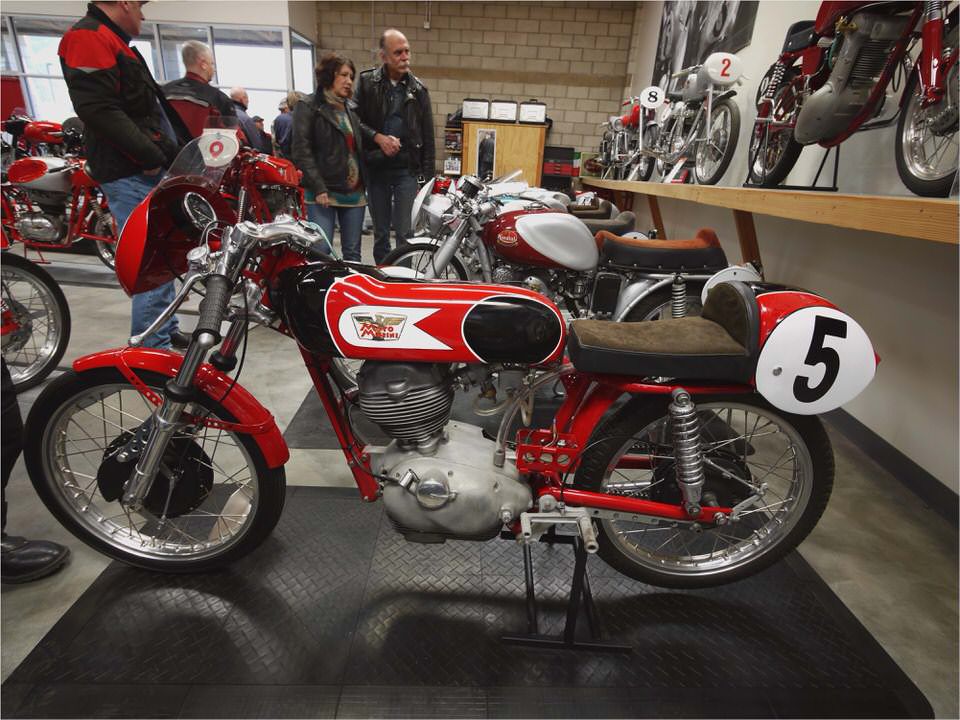
I have managed a few hours in the shed to put the bottom end of the motor together and have machined up the rear brake lever shaft, but not had time to weld it on the bike. I also had a disaster whist trying to get the front wheel bearings out. I took the circlip out and got a suitable drift and large hammer to knock the bearings out.
After a short while of bashing I realised that I was going to need some thing a little more substantial to press out these bearings. I took the wheel to a local mechanics shop that has a press and set up the wheel in the press, supported on either side of the bearing in the press. I decided to try pressing from the center race of the bearing as I wasnt exactly sure about the metal plate covering the bearing on the non circlip side.
This smashed the centre race and started moving the bearings out of their seat. I set up the press to put pressure on the outer race, applied pressure and promptly smashed the hub. I couldn’t believe it. I have never broken a hub. By their very nature they are substantial lumps of metal.
But yes, I have completely buggered my wheel. Luckily I have another, but have the same problem with that. I need to change the bearings in that too.
I will be calling Alex at NLM to find out what the hell I’m doing wrong. I will also ask him how to get the rear ones out as well, as I can’t find the circlip at all.
I have also been looking at big bore kits again and will be talking to a couple of companies about the piston crown shape of their kits to try to get one that retains the combustion chamber within the piston. It seems silly to have a flat-topped piston in a motor that should run a compact combustion space to give a high-compression ratio and quick, clean burn. I will not be buying a kit that doesn’t have a machined combustion space in its piston crown.
I also got my flywheel back from the engineer in pretty much the same condition I gave it to him. This too is made of a super hard material and can’t be machined as I wanted. I had wanted to machine 10 16mm holes in to it, remove 2.5mm from the width of the teeth and make it about half the weight of the original.
I will now have to look for someone with a surface grinder to remove the excess 2.5mm from the teeth area and I’m not sure what to do about the holes.
27/3/11
Over the past couple of weeks I have been grabbing the odd hour here and there and most of yesterday in the workshop. I have made some progress on a number of fronts. I decided not to buy a big bore kit as I have a few ideas of my own and want to investigate them first. I have taken the barrels off of the 350 Excalibur and will be using them on the race bike to start the year on.
Whilst looking at the sport and Excalibur pistons I was wondering what makes the Excalibur pistons low compression and the sport high. I got the vernier out and started to do a little measuring. It turns out that the crowns of the piston are pretty much the same only the sport ones have had between 1.2-1.4 mm more machined off of the raised section of the piston and the barrels are about the same amount shorter.
So I have taken my barrels and pistons to a local engineer and he is machining 1mm off of the top of the piston and the same off of the bottom of the barrel. This, I hope, will give me the same compression (+/-) as the sport and if it turns out that it is too low I can put a thinner base gasket in to raise it a little more. I will keep you informed on the results. Next up was the flywheel. I had it in my hand and noticed that there was no machining marks on its face.
So I got my centre punch and thought I would see how hard the metal really was. It turned out that I could centre punch a mark without much difficulty. So I divided the face in to eight and centre punched and drilled 22mm holes using normal drill bits to start and then moving on to a stepped bit that goes up to 30mm.
Here I am with my trusty drill.
basically the engineer (a different one to the one doing my pistons) hadn’t bothered trying to machining it. The net result of the lightening is a reduction from 1298 grams to 1068 grams. I will hopefully find someone with a surface grinder willing to remove 2.5mm from each side of the teeth which will reduce the weight even further.
Here is the final result before balancing.
I also tested the petrol tank for leaks. I should have done this when I welded it, but didnt.What i found when I filled the tank with water was that there where at least 10 holes from welds or where the metal had rusted away and only the paint was the barrier between the inside of the tank and the outside world. I found that as I welded the old holes, the heat would produce new holes near the weld I had just done.
After 3 hours I admitted defeat and rang a guy in Barcelona who has a load of bits for Morinis and Expecting a price that would put my wallet in to intensive care was surprised to be told that he didn’t have any 350 tanks, but had a 500 tank with no taps or cap and it was mine for 30 euros including postage. He will be checking it for leaks this afternoon and hopefully posting it in the morning. I then turned my attention to the exhaust system.
I have a diagram of a factory Morini race exhaust system and am copying it to see if it works. I have posted a copy of the diagram in to the Morini tech section. I have bought 4 mtrs of 27mm internal diameter and 30mm outside diameter tubing. The problem was that I haven’t been able to find anyone with a tube bender. I had a number of sections of chopped off Excalibur down pipe so checked the I.D and found it to be 27mm, the same as I need.
But it is double skinned tubing and, per foot weighs the same as an RSJ. Get the angle grinder out (where would I be with out my trusty angle grinder?) and make a cut down the length of the tube, but only through the outside tubing and peel the outer layer of tubing off. I then fabricate a pipe to the dimensions I need in a combination of the new tubing and the bends from the down pipes.
Sand down the welds, finish off with the drill and rotary wire brush and it looks OK. When I finish the front one I will paint them mat black.
The megaphones are under construction, but visitors stopped play for the day. I also painted the rear wheel and fitted the new tyres. This really is a big psychological boost as I have turned the corner from making everything worse by sanding or dismantling and am now seeing finished pieces that are awaiting final assembly. The front wheel turned out to be a little trickier.
It had been painted (by a blind man with a muddy stick ) and I wanted to remove this paint. I used a paint stripper and regretted it almost immediately.
It also fetched off the gold, what I thought was powder coating, but which turned out to be plastic coating, that was underneath the black. I have since spent about 4 hours stripping it all off. Well that is a lie as I got 5/8ths of the way through and couldn’t take any more.
It is now primed and has its first coat of red. I can’t put the other coats on yet as the weather is crap. I have now got a copy of the latest tech regs for the class i’m racing in. They decided not to change the eligibility date.
In fact I don’t think they have changed anything.
3/4/11
Not made a lot of progress over the weekend. I bought a roasting pan the other day to adapt in to an oil catch tray, but think I may have to buy a bigger one as it will be easier to mount outside of the frame. I also thought i would get on with the front exhaust, only to find that I don’t have any bends that are tight enough.
In the course of my working week I balanced tha carbs of the bike of a guy who has moved to the village and in the course of our conversation he happened to mention that he had a tube bender and would be willing to bend me a couple of tubes. unfortunately he went to Jerez for the GP so I didn’t get to do the exhaust.
22/4/11
Not posted for a while as I have been really busy with work and working on the Morini. I had decided to fit a thinner base gasket to raise the compression a little more, so having checked the barrels for oil ways I set about making my own thin gasket from a cereal packet (my bantams and A65′s all had cereal packet gaskets) took about 3 minutes to make the 2. I then fitted the barrels and pistons.
I didn’t have a front wheel in the bike and it was a little precarious on the stand so thought I’d fit the new front tyre to the freshly painted (about a week earlier) wheel and get the bike a little more stable. This done I fitted it to the bike and the wheels do look mighty fine. On the same day the petrol tank turned up from Barcelona and is also in very good nick.
The only bummer is that it is the later type tank and mounts on 2 rubber blobs (technical term) at the front of the frame, where as the Sport tank mounts on 2 bolts at the front of the tank. This means that I will have to get the welder out and make up some brackets for the rubber bits to sit on.I then didn’t get a chance to work on it until the beginning of this week. I dashed in to the bike shed on Tuesday and started working on the beasty.
Mainly looking at how the brakes are going to be fitted etc. fitted the primary side and then decided to get the cam belt fitted and see if I could get the motor to run. and here I am fitting the primary.
Things went well as I set all the necessary tools out along with the new cam belt and pulleys. tried to turn the crank and it turned a few degrees only to go “Donk”. I turned it backwards and again it moved only to halt with the same ominous “Donk”. Thinking I may have over done the thinness of the base gasket and that the pistons where touching the heads, I removed the heads and tried again. Donk. Bugger.
I then thought that it may be some thing on the primary side that was causing the problem. Strip all of this out and try again. Donk. Remove the barrels and the engine turns freely. OK no big deal.
Dash off to Aracena and talk to my tame engineer. In the end we turned 2mm off the bottom of the barrels to be on the safe side ( 1mm turned off the bottom flange of the barrels and 1mm for the extra thin base gasket.). Dash home and start fitting the barrels again.
By this time I have been working on the bike for 14 hours and am being summoned in to the house to kiss the kids good night.
The next day I’m up with the larks and in the shed. I am a man on a mission.I finish fitting the barrels and pistons. I could use the down pipe from the Kangaroo to get the bike started. This I feel I need as time was ticking on and there where still many things to be done before I could ride it. I needed a big boost to the enthusiasm-inator and hearing the motor would do the trick.
I had copied all the instructions out of the translated manual I have and set off to get the cam timed in. Try as I might I couldn’t get the lobes of the exhaust cam and the inlet cam to arrive at the correct intervals on the degree disc. Back upstairs to the computer and check all the data.
Everything is correct. back out to the bike shed. Take everything on the timing side off and start again. Refit everything and try to get the lobes to correspond with the data I have only to find the same thing all over again. This is getting weird.
The lobes aren’t a little out they are wildly out. In fact they have nothing to do with any of the data I have from the manual. Back upstairs to the computer. Back down stairs to the bike shed.
I then decide to count the degrees that the valves are open for. This done I find that the number of degrees that the cam should be open isn’t the same as the data is telling me. I remembered seeing a chart on the internet with all the cams listed and the duration that they are open for. Back upstairs.
Eventually find the chart on the Dutch Morini owners club site (I should really put a link to this site as it is full of useful info). From the duration of the valves I work out that I have a Strada cam fitted (huge bugger), which appears to be the mildest cam known to mankind and would mean that my motor with its flowed heads and lightened bits and bobs would probably struggle to pull the skin off of a small rice pudding.
This is really a huge downer, but still doesn’t explain why I can’t get my cam timed up. I decide to go and look at the engine from a mechanical point of view and not from the point of view of someone fitting a cam. I place the pistons at the bottom of the barrels and turn the cam in the direction stated in the manual.
I notice that as soon as the inlet has closed the exhaust opens. HHHmmmm. Thats not right. Turn the cam in the opposite (wrong) direction and count the revolutions of the cam and bingo it works. The bloody manual has been translated wrong and I’ve been trying to time my cam backwards.
By this time it has gone 10pm and I have been working on the bike for 13 hours. I’m feeling tired but am determined to get the cam fitted. Just to make doubly sure I fit the clutch and kickstart and turn the motor over with that, to assure myself which is the correct direction of rotation.
And this is where it all goes wahoony shaped. As I turn the motor over with the kick-start ( a little too enthusiastically in hindsite) there is a “DONK, DONK”. I know what Ive done and it is too late to undo it. I had left the inlet valve open on the front cylinder and smacked it with the piston.
The first donk was louder and gave more of a shock through the kickstart than the second. With out taking the head off I know I have bent the valve. I am totally drained and too tired to be angry. I go in to the house and have a couple of beers.
Go to bed and try not to think about it. The next morning I decide to sit and make a list of things to do to the Morini and where to get parts from and who is going to cut a new seat for the valve. The time scale is not good and I’m not sure who would be able to do the seat cutting. There is a company in Seville, but I’m not sure they do bike valve seat cutting.
As it happens I had done a swap for a Guzzi V50 that has no papers (it’s an ex police bike and got sold as scrap). It qualifies for the class that i want to race in and it runs. I make a list of things it would need to get it on the grid. Then check what parts I have and what I will have to buy.
The answer is that It doesn’t need much more than a set of tyres and I want to have the heads off to check the valves and to clean the ports up a little.
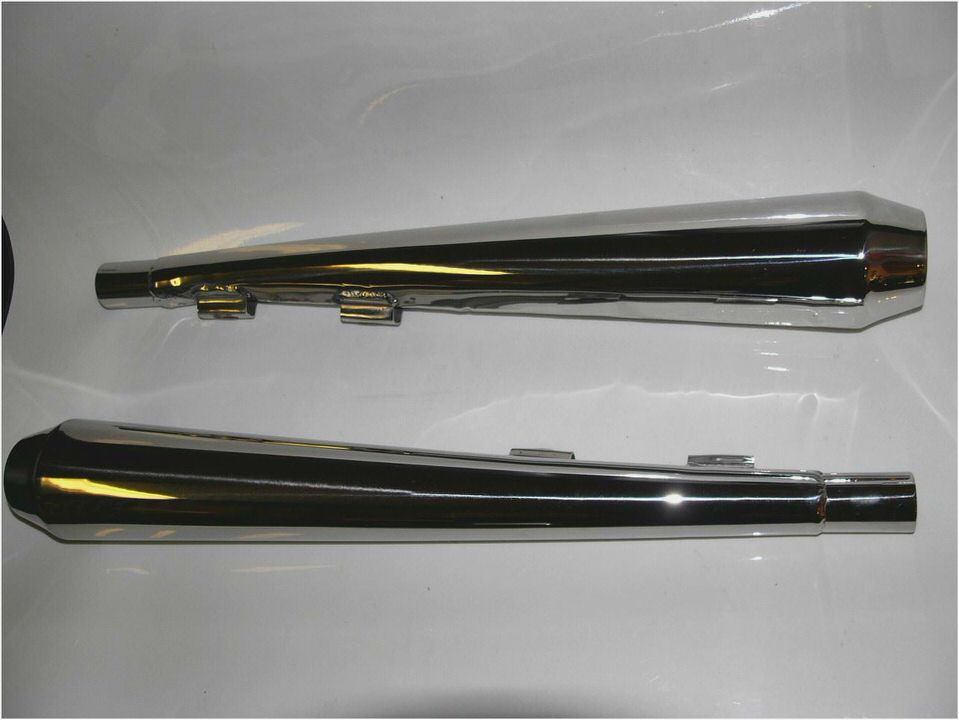
- Design from the very heart of the machine – Features – The Prague Post
- Faster and Faster: Miroslav Felgr and the story of the FGR Midalu 2500 V6
- MIDALU FGR 2500 V6 – AZURA 2008 inc.
- The Top 20 Fastest Streetfighter Bikes in the World – Hot blood
- 2005 MotoCzysz C1 Prototype Racer – Ultimate MotorCycling